Types of chips in metal cutting pdf
Types of chips in metal cutting pdf
The four forces that act upon the chip are (1) friction force, (2) normal force to friction, (3)shear force, and (4) normal force to friction. 21.13 Identify the two forces that can be measured in the orthogonal metal cutting model.
[2] Bhattacharya, A.., “Metal cutting – Theory and Practice”, Book, New Central Book Agency, Kolkata. • Microscopic study of chips frozen by drop tool or quick stop apparatus • Study of running chips by high speed camera fitted with low
theory of metal cutting • The process of metal removal, a process in which a wedge-shaped tool engages a workpiece to remove a layer of material in the form of a chip, goes back many years. Video showing the wedgeshape of different tools.
According to its name, continuous chips are formed by continuous plastic deformation of metal without fracture in front of the cutting edge of the tool and are formed …
Other less significant factors that affect chip formation are coefficient of friction and the surface finish of cutting tool. The chips produced during the machining can be broadly classified into the following types.
The type of chip formed highly depends upon the tool geometry, the material of the workpiece to be machined and machining environment. The coefficient of friction between the cutting tool and surface of workpiece also affects the chips formation process.
cutting fluids are cooling, lubrication, removing chips and metals from the tool/work piece interface, flushing, prevention of corrosion. Cutting fluids are used in machine shops to improve the life and function of cutting tools.
Types of Chips in Metal Cutting to Provide Good Surface

Different Types of Chips in Metal Cutting eligoprojects.com
A study of the nature of chip formation in metal cutting has resulted in the derivation of several basic rules which can be summarized as follows: The form of chip is unstable in most cutting
UNIT – I BASICS OF METAL CUTTING: Elementary treatment of metal cutting theory – elements of cutting process – geometry of single point tool angles, chip formation and types of chips …
The milling ram-type, manufacturing or bed type, and planer-type. Most Most machine consists basically of a motor driven spindle, whichmilling machines have self-contained electric drive motors,
During metal cutting heat generated as a result of work done .Heat is carried away from the tool and work by means of cutting fluids, which at the same time reduced the friction between the tool and chip and between tool and work and facilitates the chip formation.
1/07/2018 · in this video I have explained 3 basic types of chip forming and their effect of surface integrety, tool life etc. Comprehsive table helps to recall all the things in one platform.
16/01/2017 · On this channel you can get education and knowledge for general issues and topics.
It has one or more cutting edges, and flutes to allow fluids to enter and chips to be ejected. The drill is composed of a shank, body and point. The drill is composed of a shank, body and point. Shank: The shank is the part of the drill that is held and driven.
The following points highlight the four main types of chips formed during metal cutting. The types are: 1. Discontinuous Chip 2. Continuous Chip 3. Continuous Chip with Built Up …
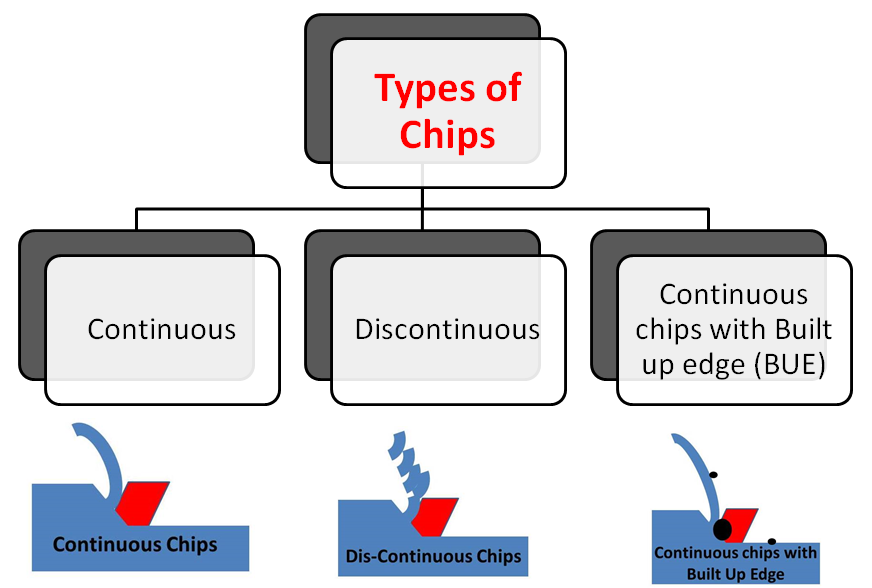
Tube fabricators use a variety of methods—sawing, lathe cutting, rotary cutting, supported shear cutting, dual-blade shear cutting, and laser cutting—to cut tubing from mill lengths into shorter pieces for use in final fabrication.
The spark metal composition test is a method of classifying steels and iron according to their composition by observing the sparks formed when the metal is held against a high speed grinding wheel.
Chip curling in metal cutting is considered. A method is proposed for determining the dimensions of the dead zone at the cutter tip on the basis of the chip’s geometric parameters.
The three types are (1) discontinuous, (2) continuous,; (3) continuous with built-up edge, which is the same as (2) except that friction at the tool-chip(4) serrated, which are semi-continuous in the sense that they possess a saw-tooth appearance
A chip breaker is a feature in the face of the insert that disrupts the flow of chips such that they break into short segments, rather than forming a long, stringy chip. 5.
The chip formation process implies that a fresh metal interface is continually produced between the tool material and the workpiece at varying cutting forces, angles and temperatures. When a cutting edge performs its metal cutting function properly, it deforms some of the workpiece material plastically and then pushes it off. Chips separate in either of three ways: they break by themselves
The chip thickness tc can be determined by knowing the depth of the cut to , and α and φ . The ratio of t o / t c is known as the cutting ratio , r , related to the two angles by:
Chip formation: During the metal cutting process, the tool removal of small metal formation from work piece is called chip.The types of chips…
Manufacturing Tooling Cutting Tool Design Nageswara Rao Posinasetti January 29, 2008 Nageswara Rao Posinasetti 2 Elements of Machining Cutting tool Tool holding Guiding device Work piece Machine tool January 29, 2008 Nageswara Rao Posinasetti 3 Chip Formation Cutting tool harder and wear resistant than the workpiece material Interference between the tool and workpiece designated as feed …

This paper looks at the process of chip formation in metal cutting as being dependent not only on the work piece material but, even on the micro and macro structures of the work piece materials.
progress in metal cutting can be associated with the introduction of high-speed steel tools by Taylor and the later use of cemented carbide tools (Schroter 1923). Each of these permitted a large increase in the rate of metal removal and
Orthogonal cutting: when chip flows along orthogonal plane, In machining like turning, shaping etc by single point turning tool, the metal removal is accomplished mainly by the principal cutting edge. But the auxiliary cutting edge also takes part in machining to some extent depending upon the auxiliary cutting edge angle, φ 1 and the magnitude of feed, s o, as indicated in Fig. 6.4. A
Analysis of Cutting Force and Chip Morphology During Hard Turning of . . . . 283 Journal of Engineering Science and Technology March 2015, Vol. 10(3)
This full featured machine has everything you need in a metal-cutting bandsaw. From its solid supporting cast iron base and quick positioning vise, to its rotary pump powered coolant system, this workhorse is at home in the hobby shop as well as the full production shop.
Swarf, also known as chips or by other process-specific names (such as turnings, filings, or shavings), are pieces of metal, wood, or plastic that are the debris or waste resulting from machining, woodworking, or similar subtractive (material-removing) manufacturing processes.
The material you’re working with and type of project you’re completing will determine which of the different types of band saws to use. Vertical , horizontal, meat, timber, and metal, cover just some of the band saws available.
Continuous chips are formed by the continuous plastic deformation of metal without fracture in front of the cutting edge of the tool and is formed by the smooth flow of the chip up the tool face. Mild steel and copper are considered to be most desirable materials for obtaining continuous chips. The chips obtained have same thickness throughout. This type of chip is the most desirable. Since it
The Nederman vertical metal chip crusher type KB accepts, crushes and breaks up bushy swarf, turnings and metal chips and at a low rotating speed the bushy swarf is cut down to small chips at a continuous rate. The metal crusher can accept large quantities and then reduce the swarf to an even flow of chips. This makes the makes crusher ideal for installation in a chip processing system. The
types of chips in metal cutting for build up edge type The built up edge formation in continuous chip is a transient and not stable of phenomenon. The accumulate build of chip metal will break away, the part adhering to the chip underside and path to the work piece.
Guide to the Different Types of Band Saws BandSawHub.com
Chips become ribbony, stringy, and difficult to dispose of 6. Degradation of surface finish 7. Increased power 8. Workpiece count 9. Cumulative cutting time. 9. 2. Tool Materials • Important properties – Toughness – avoid fracture – Hot hardness – resist abrasion – Wear resistance – solubility • Cutting tool materials – Plain carbon and low alloy steels – High-speed steels
Spiral-shaped cutting edges are cut into the side of the end mill to provide a path for chips to escape when an end mill is down in a slot or a pocket. The most common options are 2, 3, or 4 flutes.
After reading this article you will learn about:- 1. Meaning of Tool Wear 2. Types of Tool Wear 3. Causes 4. Growth 5. Forms 6. Consequences. Cutting tools are subjected to an extremely severe rubbing process. They are in metal-to-metal contact between the chip …
cutting zone into the chips, tool, workpiece and into the environment, during which, the decrease of the hardness of tool’s cutting elements, cutting wedge deformations, the loss
There are three main types Of cutting chips that Formed due to machining a work piece by using single point cutting tool either on Lathe machine Or Milling machine. Types of chips in Metal Cutting: The three common types of chip from a single point tool are.
It is important to study the types of chips produced (see Section 21.2.1 on p. 613) because they significantly influence the surface finish produced, cutting forces, as well as the overall cutting …
After reading this article you will learn about:- 1. Meaning of Metal Cutting 2. History of Metal Cutting 3. Types of Cutting Processes 4. Factors 5. Methods 6. Principles 7. Velocities. Metal cutting is “the process of removing unwanted material in the form of chips, from a block of metal, using – metal gear solid 5 staff management tutorial Chip breakers are basically of two types : • In-built type • Clamped or attachment type In-built breakers are in the form of step or groove at the rake surface near the cutting
D Different type of chips formation D Mechanism of chip formation D Problems on chip formation. D Introduction to orthogonal and oblique cutting —– History of Metal cutting research Early research in metal cutting started with in 1851. 1851 – Cocquihat – his work mainly directed towards measuring the work required to remove a given volume of material in drilling. 1873 – Hartig
An analysis of the chip geometry and the force system found in the case of orthogonal cutting accompanied by a type 2 chip has yielded a collection of useful equations which make possible the study of actual machining operations in terms of basic mechanical quantities.
Metal cut-off saw If you’re working with metal, this is the saw for you. A metal cut-off saw is best for straight cuts in all sorts of metals, particularly steel.
There are two types of metal cutting blades that most circular saws accept. The first is an abrasive, metal cut-off discs that have a mineral grit, like carbide, which line the edges of the disc allowing it to slice through metalworking projects and are designed to withstand the pressures of the task, making it more durable than a regular blade.
The right hand spiral cut of the flutes acts to force the swarf away from the cutting teeth to the rear of the flutes and out of the hole. They are better on materials which form long continuous stringy swarf, rather than chips.
The chips come out without fracture in the form of either long string or bend into a tight roll. If this chip hit finished parts of the work, it spoils the finished surface. To avoid this, a If this chip hit finished parts of the work, it spoils the finished surface.
The three kinds are just basic types of cutting. The actual cutting chips are mostly the composite form among the three; And the crumbs of blade caused by cutting is the form other than the three.
27/09/2017 · In this channel all information related to mechanical field i.e. theory , numerical problems and what ever you required related to mechanical.
These dies are used to cut the metal. They utilize the cutting or shearing action. The common cutting dies are : blanking dies , perforating dies , notching dies , trimming , shaving and nibbling dies.
Turning can produce long chips that may interfere with the work in progress. The The right cutting tools and proper lubrication are used to control chip formation.
Abrasive Water Jet Cutting – The following presentation contains facts about how abrasives are used in water jet cutting. It also provides information about the largest garnet abrasive manufacturers and exporters in India, like VV Mineral.
Discontinuous or Segmental Chips| News End Mills tool
Effect of Type of Workpiece Material on Chip Formation Process
CHIP FORMATION MECHANISM National Institute of
Metal Composition Analysis Tests and Charts Weld Guru
Manufacturing Tooling Cutting Tool Design
MECHANICS OF CHIPS FORMATION AND TYPES OF CHIPS
types of chips in metal cutting Archives TechMiny
https://en.wikipedia.org/wiki/Chip_formation
PPT – Metal Cutting PowerPoint presentation free to view
– Swarf Wikipedia
11 Name and briefly describe the four types of chips that
Name and briefly describe the four types of chips that
Read Your Chips Modern Machine Shop
3/4 B.Tech. FIFTH SEMESTER ME5T2 METAL CUTTING & MACHINE
Vertical metal crusher type KB for chips swarf and
Manufacturing Tooling Cutting Tool Design Nageswara Rao Posinasetti January 29, 2008 Nageswara Rao Posinasetti 2 Elements of Machining Cutting tool Tool holding Guiding device Work piece Machine tool January 29, 2008 Nageswara Rao Posinasetti 3 Chip Formation Cutting tool harder and wear resistant than the workpiece material Interference between the tool and workpiece designated as feed …
During metal cutting heat generated as a result of work done .Heat is carried away from the tool and work by means of cutting fluids, which at the same time reduced the friction between the tool and chip and between tool and work and facilitates the chip formation.
The material you’re working with and type of project you’re completing will determine which of the different types of band saws to use. Vertical , horizontal, meat, timber, and metal, cover just some of the band saws available.
Tube fabricators use a variety of methods—sawing, lathe cutting, rotary cutting, supported shear cutting, dual-blade shear cutting, and laser cutting—to cut tubing from mill lengths into shorter pieces for use in final fabrication.
It is important to study the types of chips produced (see Section 21.2.1 on p. 613) because they significantly influence the surface finish produced, cutting forces, as well as the overall cutting …
The three kinds are just basic types of cutting. The actual cutting chips are mostly the composite form among the three; And the crumbs of blade caused by cutting is the form other than the three.
theory of metal cutting • The process of metal removal, a process in which a wedge-shaped tool engages a workpiece to remove a layer of material in the form of a chip, goes back many years. Video showing the wedgeshape of different tools.
It has one or more cutting edges, and flutes to allow fluids to enter and chips to be ejected. The drill is composed of a shank, body and point. The drill is composed of a shank, body and point. Shank: The shank is the part of the drill that is held and driven.
The chips come out without fracture in the form of either long string or bend into a tight roll. If this chip hit finished parts of the work, it spoils the finished surface. To avoid this, a If this chip hit finished parts of the work, it spoils the finished surface.
16/01/2017 · On this channel you can get education and knowledge for general issues and topics.
Spiral-shaped cutting edges are cut into the side of the end mill to provide a path for chips to escape when an end mill is down in a slot or a pocket. The most common options are 2, 3, or 4 flutes.
There are two types of metal cutting blades that most circular saws accept. The first is an abrasive, metal cut-off discs that have a mineral grit, like carbide, which line the edges of the disc allowing it to slice through metalworking projects and are designed to withstand the pressures of the task, making it more durable than a regular blade.
VLFVLQPHWDOFXWWLQJ IOPscience
11 Name and briefly describe the four types of chips that
CHIP FORMATION MECHANISM National Institute of