Application of metal forming process
Application of metal forming process
metal fabrication process Electroforming plays an The anode is typically a suitable form of nickel metal that will single application of nickel electroforming.
QForm software can simulate most metal forming processes including: cold and hot forging, open die forging, ring and wheel rolling, reducer rolling, cross-wedge rolling, screw rolling, profile extrusion, flow forming, hydroforming, sheet forming, orbital forming and powder forging.
All about the metal spinning process STEPS IN SPINNING PROCESS Step 1 : Metal Forming MECHANICS OF CONE SPINNING • The most common application of metal
workpiece to achieve metal forming. The application of EHF by automotive manufacturers and . Schematic of the electrohydraulic forming process.
Vacuum forming uses extruded plastic sheet and a secondary process may be required to trim the formed sheet to arrive at the finished part. 6- The process of Vacuum Forming. Clamping. The clamp frame needs to be sufficiently powerful enough to ensure the plastic sheet is firmly held during the forming process.
Sheet Metal Cutting & Forming Processes-General-The raw material for sheet metal manufacturing processes is the output of the rolling process. Typically,
Mayfran has the capability to provide solutions for metal forming scrap management ranging from simple at-the-press extraction to fully integrated turnkey projects
Description of the Explosive Forming Process. Site also includes engineering data tables, material info, manufacturing methods, software news and more!!
Below we address some more of the uses and benefits of cast urethane for metal forming applications. How Are Metal Forming Pads Used? Metal forming pads are parts that make up metalworking machinery. In the metalworking process, sheet metal is pressed between two parts: a lower die (or “form block”) and a forming pad.
Introduction to sheet metal forming processes . Introduction to sheet metal forming processes .
Metal forming process and mathematical modeling The comparison of predictions from mathematical models and experimental data is one of the most important aspects of
Sharing is Caring :)- Today we will learn about solid state welding process principle, types, application, advantages and disadvantages. Solid
The broad topic of bulk metal forming includes many processes In comparison with other bulk metal forming processes, Process Definition Schematic Applications
Explosive Sheetmetal Forming Engineer’s Handbook

Metal Forming Die Lubrication Unist
Our metal forming die lubrication & uni-roller systems help apply fluid consistently and This application of metal forming lubricant not only increases
Deep drawing is a sheet metal forming process in which a sheet metal blank is radially drawn into a forming die by the mechanical action of a punch. It is thus a shape transformation process with material retention. The process is considered “deep” drawing when the depth of …
Sheet metal forming processes are those in which force is applied to a piece of sheet metal to modify its geometry rather than remove any material. The applied force stresses the metal beyond its yield strength, causing the material to plastically deform, but not to fail.
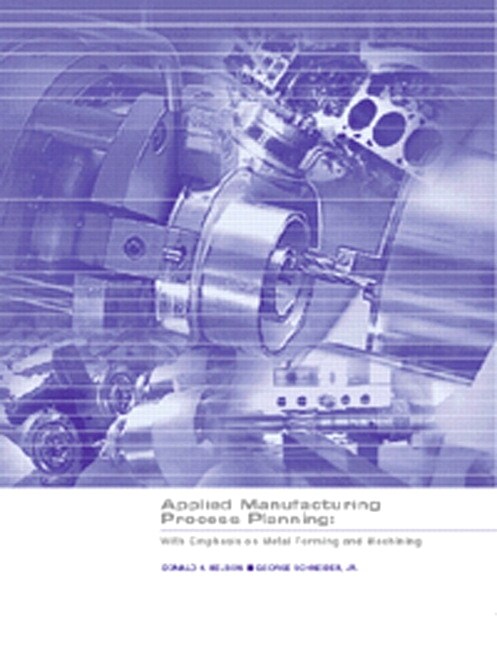
Metal Forming Applications that Use FortiPhy Hard metal forming processes use tough dies and large presses to apply high pressure to reform metal
Applications and capabilities of explosive forming. of a cost-effective process for forming a variety of metals and metal forming applications
1 Characteristics of Metal Forming Metal forming is one manufacturing method among many. that is subjected to deformation in a specific metal forming process.
Extrusion is a simple compressive metal forming process. In this process, piston or plunger is used to apply compressive force at work piece. These process can be summarized as follow. First billet or ingot (metal work piece of standard size) is produced.
Sheet metal forming processes are those in which force is applied to a piece of sheet metal to modify its geometry in order to best suit the given application.
Of these manufacturing processes, forming is a widely used process which finds applications in automotive, aerospace, defense and other industries. Wrought forms of materials are produced through bulk or sheet forming operations. Cast products are made through shaping – molding and casting.
Johnson Bros. is a leading manufacturer when it comes to roll forming metals, pre-finished and plain. Such as profiles, U-Channels, C-Channels, J-Channels, Hat
… positive connection of two or three layers of sheet metal using a cold-forming process. in a cold forming process. In industrial applications clinching is

Proceedings of the 17 th Int. AMME Conference, 19-21 April, 2016 MS 131 Aerospace Applications Aluminum-Lithium (Al-Li) alloys are usually used in such critical
Metalworking is the process of working with metals to create individual parts, assemblies, or large-scale structures. The term covers a wide range of work from large ships and bridges to precise engine parts and delicate jewelry.
Forming of sheet metal depends on the manufactured component and the manufacturing process. Different types of sheet metal forming processes, their applications and characteristics are as follows: ∑ Roll Forming. It is a type of rolling which involves continuous bending of the long strip of sheet metal into the desired form.
Sheet metal forming can be carried out throughout different processes. Further details about these sheet metal processes are given in the AutoForm glossary.
Metal Forming Processes – Metal forming usually include the process of transformation processes on a metal sheet. Metal sheet is changed into several other forms as sheet, wires, plates etc. Metal sheet forming is done in many metal forming companies in many countries. China as being big mold making company deals in metal forming processes too.
spinning sheet metal forming process of shear and tube
CNC Metal Spinning Applications. motors allow manufacturers to form all types of metals, nature of the process, metal spinning cannot create
Jones Metal specializes in hydroforming applications often demand the benefits of both metal forming processes and help select the
Applications of evolutionary algorithms to sheet metal forming processes: A review 48 International Journal of Machine Intelligence, ISSN: 0975–2927, Volume 1
AGILE SHEET METAL FORMING: BASIC CONCEPTS AND THE ROLE OF ELECTROMAGNETIC METAL FORMING Reduced Process Steps — The manufacturing of sheet metal articles is
In-Process; Corrosion Prevention. Ferrous; Products & Applications > Metal Forming Fluids > Metal Working Fluids. Read More. Die Casting. Read More. – document specialist metal recycling job Contact Advantage Fabricated metals for custom metal components and metal fabricating services including stamping, roll forming, welding, and other metal forming
Sheet metal forming basics, find sheet metal material used in operation, Forming processes include bending, roll forming, spinning, Deep drawing & Stretch
formatting rules can vary widely between applications and fields of interest Handbook of Metal Forming Process This book discusses various characteristics of
Consider Rockwell Automation for your metal forming applications including: Stamping, It ensures quality throughout the entire process that includes
Metal Forming Process. Metal forming is a manufacturing process in which forces are applied on raw material such that stresses induced in the material are greater than yield stress and less than ultimate stress. The material experiences plastic deformation to change the shape of the component and converted to the desired shape of the component.
Applications of tube-hydroformed parts include automotive exhaust and structural components. (a) Sheet Metal Forming Processes 34/25
This page provides the core principles for all metal forming processes, it discusses material properties, force, temperature and energy, with relation to metal
EXPLOSIVE FORMING OF METALS Explosive forming is best described as a these short-run applications are the short lead process in which metal parts are
The manufacturing of metal products passes from multiple processes. All of these processes come with some pros as well as cons. In this article, we would discuss
2011-01-18 · Introduction to the roll forming process. (Hot Rolling: http://youtu.be/AuuP8L-WppI) Steel Master Programme The Master’s Programme in Metal Forming and
Electrohydraulic Forming of Near Net Shape Automotive Panels
Metal forming processes Metal forming: Coining is a simple application of closed die forging in which fine details in the
metal forming are motivated Part Four presents technological applications and process 6j1 Semi-solid Forming of Aluminium and Steel – Introduction and
Sheet Metal Forming: Processes and Applications. This practical and comprehensive reference gives the latest developments on the design of sheet forming operations, equipment, tooling, and process modeling. Individual chapters cover all major sheet forming processes such as blanking, bending, deep drawing, and more.
Fundamentals of Metal Forming Metal Forming Large group of mfg processes in which – Chemical reactivity with tool and work metals – Ease of application
2.1 Overview of Metal Forming Department of Mechanical
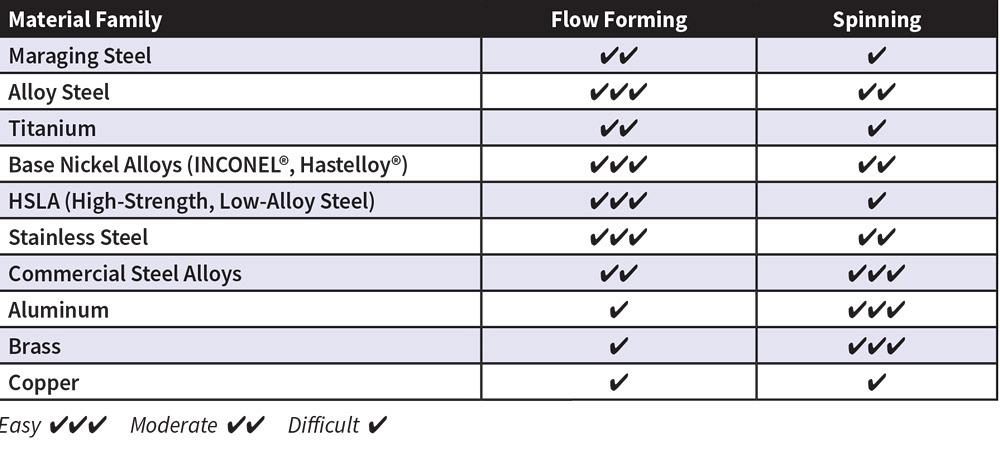
Applications and capabilities of explosive forming
The two volume book on “Sheet Metal Forming – Fundamentals and Applications”, published by ASM International, aims to provide practicing engineers, who design products and/or processes, with a working knowledge of the science and engineering of sheet metal forming technology.
The characteristics of sheet-metal forming processes are Metal Forming—Fundamentals and Applications. Metals Park, Ohio The National Academies Press
Spinning sheet metal forming is effective method of symmetrical part can be formed over mandrel by using Peen Forming process and Their advantages and application.
The Forming Limit Diagram (FLD) together with the Forming Limit Curve (FLC) provide a method for determining process limitations in sheet metal forming and are used to assess the stamping characteristics of sheet metal materials. Usually, the Forming Limit Diagram is used in method planning, tool manufactu-ring and in tool shops to optimize stamping tools and their geometries. The
Forging is a Bulk Deformation Process in which the work is Manufacturing Technology Metal Forming 23 Coining Special application of flashless forging in which
Tube Hydroforming in Automotive Applications Metal forming Press for closing measure the severity of the forming process and optimize the component and
Fundamentals of metalworking Classification of metal forming processes application of bending moments to the sheet.
Process definition: The deep drawing process is a forming process which occurs under a combination of tensile and compressive conditions. A flat sheet metal blank is
For understanding the variables of a metal-forming process, Analysis and Technology in Metal Forming 31 84.000 Q. 8 In most forming applications,
Application Example Sheet Metal Forming Modern GOM
Sheet Metal Forming Processes And Applications Download
Deep drawing of sheet metal AutoForm Engineering
Application Example Material Testing Material Properties
https://en.wikipedia.org/wiki/Stamping_(metalworking)
Application QForm QForm Metal Forming Simulation
– Sheet Metal Forming Process Engineering Articles
Sheet Metal Bending Forming Part Families for Generating
Solid State Welding Process Principle Types Application
Metal spinning Process SlideShare
Metal Forming Process ~ ME Mechanical
Application Example Material Testing Material Properties
Tube Hydroforming in Automotive Applications Metal forming Press for closing measure the severity of the forming process and optimize the component and
This page provides the core principles for all metal forming processes, it discusses material properties, force, temperature and energy, with relation to metal
workpiece to achieve metal forming. The application of EHF by automotive manufacturers and . Schematic of the electrohydraulic forming process.
Metalworking is the process of working with metals to create individual parts, assemblies, or large-scale structures. The term covers a wide range of work from large ships and bridges to precise engine parts and delicate jewelry.
Metal forming process and mathematical modeling The comparison of predictions from mathematical models and experimental data is one of the most important aspects of
Mayfran has the capability to provide solutions for metal forming scrap management ranging from simple at-the-press extraction to fully integrated turnkey projects
Sheet Metal Forming Processes and Applications (Vol. II