Shearing process in sheet metal pdf
Shearing process in sheet metal pdf
The raw material for sheet metal manufacturing processes is the output of the rolling process. Typically, sheets of metal are sold as flat, rectangular sheets of standard size. Therefore the first step in any sheet metal process is to cut the correct shape and sized ‘blank’from larger sheet.
19/06/2014 · The sheet metal shearing segment shows the shearing process while explaining and defining blade rake/shear angle, blade/knife clearance, blade/knife angle of …
whole shearing process starting with the elastic stage and ending with the total separation of the sheet metal. Blanking process, which is also referred to as shearing, or punching process, is illustrated in Fig. . A metal sheet is pressed on a die by a blank holder and perforated by a punch. Four characteristic dimensions can be distinguished on the blanked edge such as the roll over depth
Blanking is a cutting process in which a piece of sheet metal is removed from a larger piece of stock by applying a great enough shearing force. In this process,
Sheet Metal Sheering Shearing is a fabricating process that is used to cut straight lines in sheet and plate material. The process allows for material to be cut …
Shearing is separating sheet metal by moving cutting tools parallelly, with a short gap, by shearing off the metal sheet between the tools. Depending on the shear strength of the used metal sheet high cutting forces are necessary to separate the material.
The sheets are nally seperated by a ductile fracture process. Again there is a di erence between station- Again there is a di erence between station- airy and transient shearing processes.
Shearing Parameters • Clearance, c, between the punch and die typically between 2% and 10% of sheet metal thickness • As clearance increases, sheared edge becomes rougher
the sheet metal with the required shearing force. It is considered as 1/3 of thickness of the sheet metal [7]. Secondary Distance Moved by Tool (H2). This is the distance moved by tool through the sheet metal with the required deformation force. 3.2 Classification and Extraction of Edges Edges of the reference face in a part model are classified as CEE, IEE, CIE and IIE as explained in sub
Chapter 4-The Shearing Process. The use of shears in sheet metal production has diminished through the use of cut-off tooling in CNC punching and the use of shake-out technology to separate parts from the sheet skeleton.
Bending and shearing methods. The bending process in metals, especially sheet metals has to be carried out in a highly technical way. One of the technologies that are employed for cutting sheet metals is the sheering process which is processed in terms of …
In principle, it does not matter whether you want to process: sheet metal, plastics, cardboard, textiles or foils. Do you want: closed or open cuts, forming cuts (even/planar and solid cut edges), single or several piercing holes with one stroke or Piercing + feeding + calibrating with one stroke?
Lecture 5. SHEARING Shearing is a cutting operation used to remove a blank of required dimensions from a large sheet. To understand the shearing mechanism, consider a metal being sheared between a punch and a die, Fig 5.1 Typical
shear stress, which has its highest value at 45 ° to the axis of loading. For polymers, the elastic limit is the stress at which the uniaxial stress-strain curve becomes …
sheet metal is sheared between two shear tools and held in place by clamps. Here, the geometric properties defined are sheet thickness h , clearance c and shear tool radius r .
Shearing is a metal fabricating process used to cut straight lines on sheet metal. Material is cut (sheared) between the edges of two opposed cutting tools.
sheet metal thickness, blank holder force to be in two levels (0, 3000N) and sheet metal thickness to be in four levels (0.5, 0.6, 0.7, 0.8)mm. Perform a factorial experimental design …
Shearing machines (sheet metal) require periodic maintenance. Shear blade sharpening must be performed on a regular basis so that shears do not yield poor quality cuts. In addition, the proper equipment must be used for shear sharpening. With shear blades, the angle of the cutting edge and the finish of the grind are important factors in determining shear performance and longevity. Often
Shearing, also known as die cutting, is a process which cuts stock without the formation of chips or the use of burning or melting. Strictly speaking, if the cutting blades are straight the process is called shearing; if the cutting blades are curved then they are shearing-type operations. [2]
YouTube Embed: No video/playlist ID has been supplied
High performance magnetic pulse technology for sheet metal
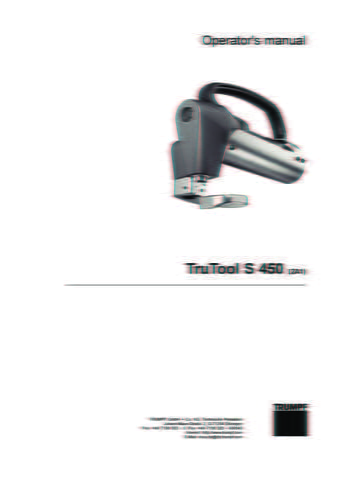
A Predictive Model Construction for the Sheared Planes in
Fine blanking is a sheet metal process producing smooth -sheared edges over the full workpiece thickness in one single action, whilst conventional blanking results in an
The term punching describes a shearing process, in which a punching machine separates a sheet of metal by striking it, while supporting it by a die with a hole matching the cross section of the punch.
Shearing: This is nothing but cutting of sheets by shearing action. Sheet forming: Sheet metal forming involves forming and cutting operations performed on metal sheets, strips, and coils.
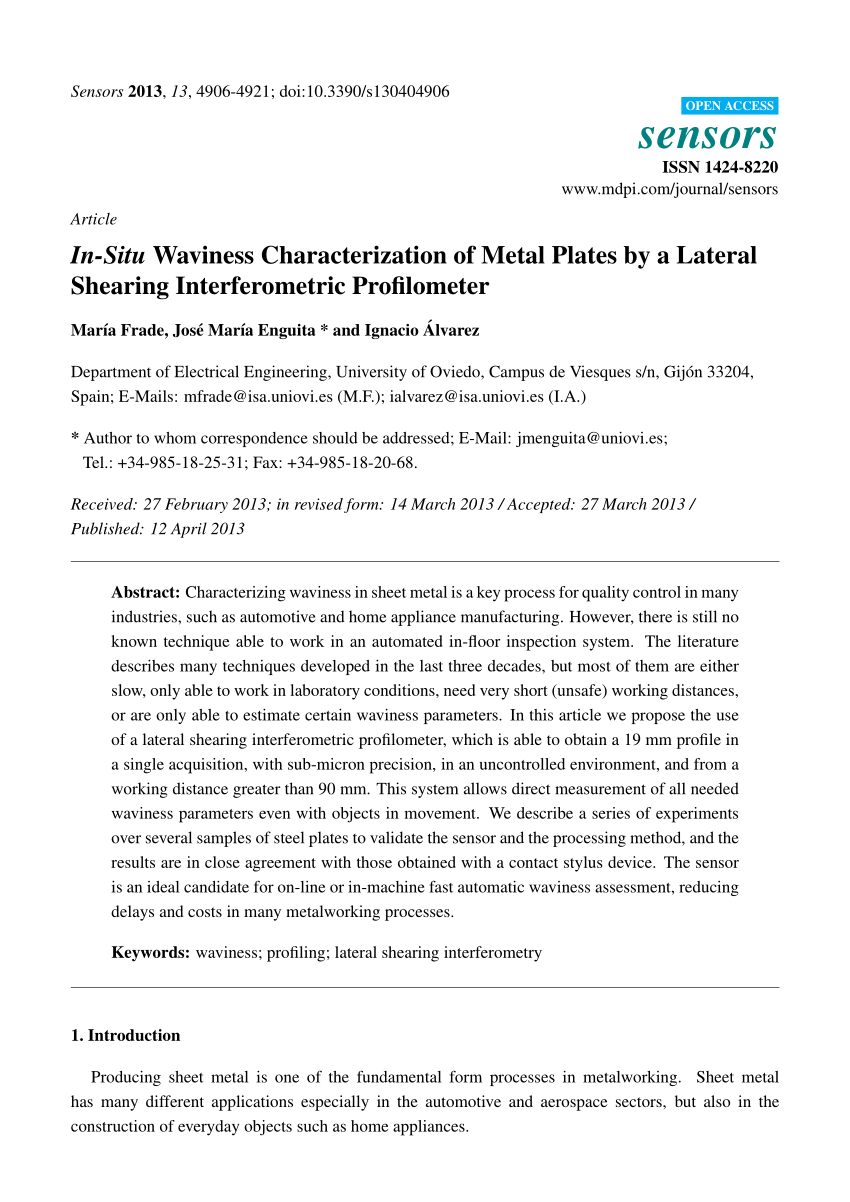
Shearing is a process which cuts stock without the formation of chips or the use of burning or melting. The most commonly sheared materials are in the form of sheet metal or plates.
Metal cutting is a process used for separating a piece of material of predetermined shape and size from the remaining portion of a strip or sheet of metal. It is one of the most extensively used processes throughout die and sheet-metal work. It consists of several different material-parting operations, such a piercing, perforating, shearing, notching, cutoff, and blanking.
Shearing is a metal fabricating process used to cut straight lines on flat metal stock. During the shearing process, an upper blade and a lower blade are forced past each other with the space between them determined by a required offset. Normally, one of the blades remains stationary.
EDPT 604. Metal Forming Processes and Machines Lecture 7 Shearing of Metals Dr. Mohamed Harraz 2013 1 Sheet Metalworking • Cutting and forming operations performed on
Shearing. Shearing is a process for cutting sheet metal to size out of a larger stock such as roll stock. Shears are used as the preliminary step in preparing stock for stamping processes, or smaller blanks for CNC presses.
Shearing is a fabricating process that is used to cut straight lines in sheet and plate material. The process allows for material to be cut into shorter lengths than a conventional cut-to-length line.
1 Lecture 4. Sheet metal processing The raw material for sheet metal manufacturing processes is the output of the rolling process. Typically, sheets of metal are sold as flat, rectangular sheets …
An Application of Response Surface Method in the
6 Sheet Metal Cutting Cutting of metal between die components is shearing process in which the metal is stressed in shear between two cutting edges to …
Metal Shearing Services Sometimes, metal sheets are required to be cut in square rectangular shapes, with certain thicknesses and lengths without forming chips or without burning or melting. You can achieve this by employing the easiest and most suitable process – metal shearing. However, you may need to partner with a reputed and industry
Background Shearing is a fast and inexpensive method to cut sheet metal that has been used since the beginning of the industrialism. Consequently, published experimental studies of shearing can be
Shearing process These categories are: 1) Direct – compression – type process 2) Indirect – compression processes 3) Tension type processes 4) Bending processes 5) Shearing processes Sheet metal processing The raw material for sheet metal manufacturing processes is the output of the rolling process. Typically, sheets of metal are sold as flat, rectangular sheets of standard size. If the
of Sheet Metal Blanking Process Galal Mohamed Elkharraz (Department of Industrial and Manufacturing system Engineering, University of Benghazi, Libya) Abstract: The blanking process used in the manufacturing industry constitutes the first stage of any forming process, which is a widely used process in high volume production of sheet metal components. The main problem faced designers …
18/10/2012 · This video explain the operations of shearing and bending metals and the important factors that each process depend on it. Sheet Metal Forming – Round
The objective for this project was to develop a high speed adiabatic shearing process, which will solve the problems that the automotive industry has today with punching holes in steel sheet metals. – composite materials fabrication handbook 1 pdf The Shearing Process in Metal Fabrication Blog March 29th, 2017. Metal fabrication is a broad term for a combination of processes to construct structures, items and machines from raw metallic material.
SHEARING Shearing is a cutting operation used to remove a blank of required dimensions from a large sheet. To understand the shearing mechanism, consider a metal being sheared between a punch and a die, Fig 5.1 Typical features of the sheet and the slug are also shown in this figure.
The set up of the LM1010 Mechanical Shears is a critical process and one which is more involved than the LM1014 model. We speak from experience in stressing the ,500.00 Factory serviceman set up as an option worth the money.
Abstract. The developed hybrid laser-assisted shearing process enables conventional punching machines to produce punch-sheared edges with continuous clear-cut surfaces in stainless steel plates (1.4301), spring steel plates (1.4310), and titanium alloy plates (3.7165).
The sheet metal cutting shearing process is performed on a shear machine, often called a squaring shear or power shear, that can be operated manually (by hand or foot) or by hydraulic, pneumatic, or electric power. A typical shear machine includes a table with support arms to hold the sheet, stops or guides to secure the sheet, upper and lower straight-edge blades, and a gauging device to
The shearing processes such as the blanking and piercing of sheet metals have been often used to prepare workpiece for subsequent forming operation. The sheared plane plays an important role in the shearing products’ dimension precision and their functions. The quality of sheared plane is affected not only by the material characteristics but
Blanking operation is widely used to cut sheet or plates by a shearing process between punch and die. The pro- cess of shearing and the conditions of the sheared surface are influenced by the
Shearing Process 1. Punching: shearing process using a die and punch where the interior portion of the sheared sheet is to be discarded. 2. Blanking: shearing process using a die and punch where the exterior portion of the
©2007 John Wiley & Sons, Inc. M P Groover, Fundamentals of Modern Manufacturing 3/e Shearing Sheet metal cutting operation along a straight line between two cutting edges • Typically used to cut large sheets Figure 20.3 Shearing operation: (a) side view of the shearing operation; (b) front view of power shears equipped with inclined upper cutting blade.
Unlike sheet metal forming such as deep drawing and punch stretching, the elements in the shearing region undergo very large plastic deformation and this makes it difficult to do accurate simulation of the shearing process of sheet metal. To overcome this problem, remeshing of elements must be repeated often in the simulation process.
A failure during sheared edge stretching depends on prior deformation in the sheet, the shearing process, and the subsequent strain path in the SAZ during stretching. Data from laboratory hole
Within the sheet metal industry, different shear cutting technologies are commonly used in several processing steps, e.g. in cut to length lines, slit- ting lines, end cropping etc. Shearing has speed and cost advantages over
Sheet Metal Shearing & Bending YouTube
An Overview of Clearance Optimization in Sheet Metal
Finite element simulation of the shearing mechanism in the
Shearing (manufacturing) Wikipedia
Chapter 4- The Shearing Process Make it Metal
Metal fabrication shearing metals process
Oscillation overlaid shearing of sheet SpringerLink
https://en.wikipedia.org/wiki/Shear
(PDF) Effects of Blanking Speed on the Shear Surface of
engrenages conception fabrication mise en oeuvre pdf – Metal Shearing Services Shear – Alliant Metals Inc.
Shearing Machines (sheet metal) Information Engineering360
3-D MODELLING OF SHEET METAL SHEARING H.H. Wisselink and
YouTube Embed: No video/playlist ID has been supplied
Lect 7 Shearing of Metals.pdf Sheet Metal Process